Everything You Should Know About Inventory Management
In today’s highly competitive market landscape, mastering inventory control is pivotal to the success of businesses, both large and small. Effective inventory management ensures that there’s always the right amount of stock available to meet demand without tying up excess capital in surplus goods. It requires a precise balance between stock availability and cost control to avoid issues like stockouts and overstocking, both of which can harm a business’s bottom line. So, allow our experienced Boise moving and storage team of experts to advise you on all you should know about inventory management.
What is Inventory Management?
Inventory management is the backbone of any successful business that deals with goods. Basically, it ensures a seamless flow of products from suppliers to customers. It encompasses the process of efficiently monitoring, tracking, and controlling inventory levels to meet demand without overstocking or understocking. By maintaining accurate records and using inventory control software, businesses can gain real-time visibility into their stock.
This enables informed decision-making and avoids costly stockouts or excess inventory. Effective stock control optimizes cash flow, reduces carrying costs, and enhances customer satisfaction through timely order fulfillment. Additionally, it aids in identifying slow-moving or obsolete items. This makes it possible for businesses to clear them out and make room for more profitable products. Mastering inventory optimization can lead to increased profitability and a competitive edge in the market.
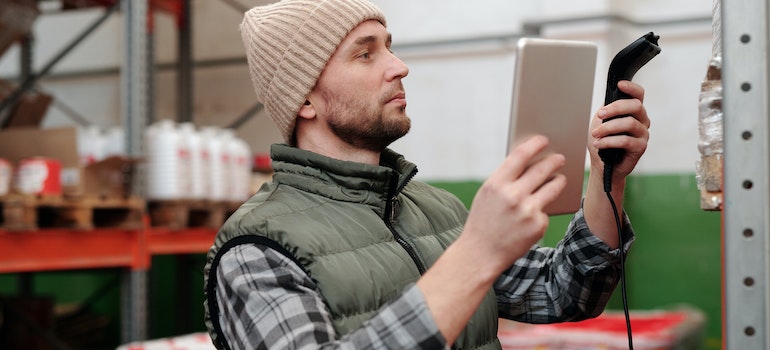
Understanding the Importance of Assets Management
It is crucial for businesses to maintain a balanced supply of products and meet customer demands efficiently. Also, it is beneficial for optimizing financial resources, ultimately leading to improved profitability and operational success.
Cost Management
Cost control in inventory management is vital for businesses to strike the right balance between maintaining sufficient stock levels and minimizing expenses. By optimizing inventory turnover and avoiding overstocking, companies can reduce carrying costs, such as storage fees and obsolescence charges. Effective cost management also helps prevent stockouts and the associated lost sales, ensuring customer satisfaction and loyalty.
Employing inventory optimization techniques, such as just-in-time (JIT) inventory or economic order quantity (EOQ), enables businesses to streamline their supply chains and make informed decisions, contributing to overall financial efficiency and profitability. This is highly important if you decide to relocate.
Improvements in Cash Flow
Improved cash flow is a significant benefit of efficient inventory control. When they optimize stock levels and reduce excess inventory, businesses can free up valuable working capital that would otherwise be tied up in idle goods. This surplus cash can be reinvested in crucial areas like research and development, marketing, or expansion initiatives.
Moreover, minimizing stockouts through better inventory control ensures consistent sales and revenue generation, further strengthening the cash flow. With a well-managed inventory system, businesses can enhance their financial liquidity. Also, they can respond to market changes effectively and maintain a healthier bottom line.
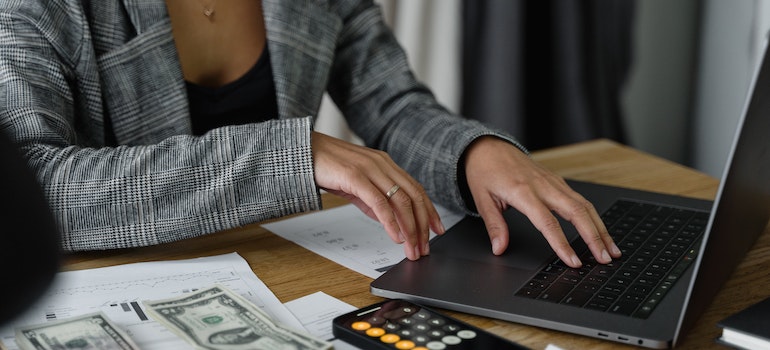
You should know that there are several types of inventory
Inventory management involves handling various types of inventory, each serving a distinct purpose within a business. Understanding and categorizing these inventory types are essential for efficient operations and ensuring a smooth supply chain. Businesses must recognize the unique characteristics of each inventory type to implement appropriate management strategies that align with their specific needs and goals.
Management of Raw Materials
Raw materials represent a crucial type of inventory in the production and manufacturing sectors. They consist of the basic components and materials required to create finished goods. Proper management of raw materials is essential for uninterrupted production and timely order fulfillment. Naturally, Idaho storage solutions are always at your disposal for this purpose. Maintaining adequate levels of raw materials is vital to avoid production delays and to capitalize on economies of scale when purchasing in bulk.
Moreover, effective inventory control of raw materials can help businesses reduce the risk of stockouts and ensure consistent product quality. Keeping a close eye on supplier relationships and lead times is also crucial in managing raw material inventory. It enables businesses to plan for fluctuations in demand and maintain a steady supply chain.
Understanding WIP
Work-in-progress (WIP) represents a critical type of inventory that denotes products in various stages of production. It includes partially assembled goods that have not yet reached the final stage of completion. Effective management of WIP is essential to ensure smooth production flow, reduce bottlenecks, and meet production deadlines. Maintaining optimal levels of WIP allows businesses to respond quickly to changes in demand and adapt to market fluctuations.
Monitoring WIP closely enables the identification of potential issues in the production process, facilitating timely adjustments and quality control. You may benefit from relying on some of the best storage pods Boise offers in this situation. Additionally, by efficiently managing WIP, businesses can minimize carrying costs, improve resource allocation, and enhance overall productivity. Emphasizing WIP management fosters better synchronization across production departments, streamlines workflows, and ultimately contributes to maximizing output and meeting customer expectations.
Finished Goods Management
Finished goods are the end products that are ready for sale and distribution to customers. As a critical type of inventory, proper management of finished goods is essential for meeting customer demand efficiently and ensuring on-time delivery. Maintaining optimal levels of finished goods is crucial to avoid stockouts and capitalize on sales opportunities. Effective inventory control allows businesses to keep a close eye on product turnover rates. If you use commercial storage, they are going to be at your disposal whenever you need them.
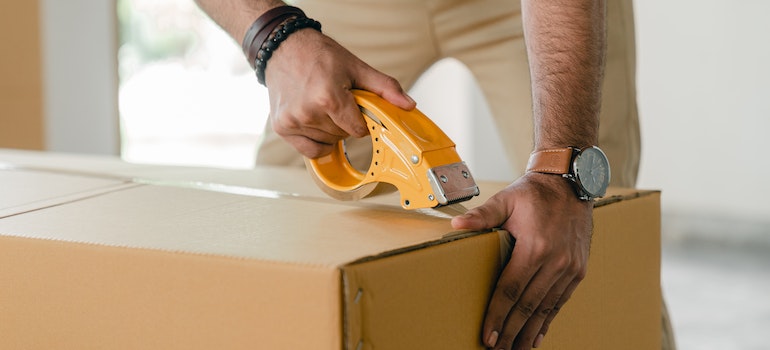
It enables them to identify popular items and adjust production accordingly. Additionally, monitoring finished goods inventory aids in identifying slow-moving products, which can then be discounted or marketed differently to clear stock. Proper storage and handling of finished goods are also essential to preserve product quality and minimize the risk of damage. As you can see, with good management of finished goods, businesses can enhance customer satisfaction, minimize carrying costs, and boost overall profitability.
Managing MRO goods
MRO (Maintenance, Repair, and Operations) goods constitute a significant type of inventory. They encompass various supplies and materials essential for supporting daily business operations and ensuring equipment functionality. These items are not directly incorporated into the final product but play a crucial role in maintaining smooth business functioning. MRO inventory includes items like tools, cleaning supplies, spare parts, and safety equipment.
Proper management of MRO goods is vital to prevent production downtime, reduce equipment repair delays, and enhance workplace safety. In fact, you can benefit from using commercial mobile storage in a situation of this kind. Regularly monitoring MRO inventory levels helps businesses avoid stockouts and overstocking, optimizing cash flow. Establishing efficient procurement processes for MRO goods ensures timely availability when needed, preventing disruptions in production and operations. Careful management of MRO inventory streamlines business processes, minimizes operational risks and contributes to overall cost-effectiveness.
Exploring Different Techniques
In inventory control, various techniques are employed to handle and control inventory effectively. Each technique offers distinct approaches to optimize stock levels, streamline operations, and meet customer demands efficiently. Understanding these diverse inventory management techniques allows businesses to tailor their strategies to specific needs and industry requirements.
The ABC Technique
The ABC analysis is a widely used inventory optimization technique that classifies inventory items into three categories: A, B, and C, based on their value and importance.
- Category A includes high-value items that contribute significantly to revenue but represent a relatively small portion of the total items.
- Category B comprises moderate-value items, falling in between Category A and C in terms of importance.
- Category C includes low-value items with high quantities but minimal impact on revenue. This approach optimizes resource allocation, reduces carrying costs, and ensures optimal inventory control throughout the supply chain.
The JIT Method
The Just-in-Time (JIT) method is a stock management technique designed to streamline production and minimize excess inventory. In JIT, items are procured and produced only when they are needed, eliminating the need for stockpiling. This approach aims to reduce carrying costs, optimize space utilization, and enhance cash flow.
Suppliers play a crucial role in JIT, delivering materials to manufacturers precisely when required, and ensuring a continuous production flow. JIT fosters a lean and efficient supply chain, as it emphasizes real-time demand responsiveness and minimizes the risk of stockouts or obsolete inventory. When using this method, businesses can achieve cost savings, improve operational efficiency, and respond swiftly to changing market demands.
The EOQ Assets Management Technique
The Economic Order Quantity (EOQ) is a fundamental stock management technique that determines the optimal order quantity to minimize total inventory costs. EOQ takes into account the balance between ordering costs (such as setup, shipping, and handling) and carrying costs (such as storage and holding expenses). The goal of EOQ is to strike the right balance, ensuring that the order quantity minimizes both types of costs.
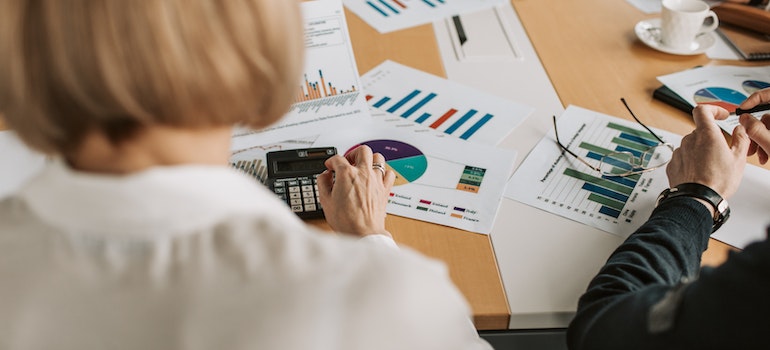
By calculating the EOQ, businesses can avoid overstocking and stockouts, leading to reduced carrying costs and increased operational efficiency. Implementing EOQ helps businesses make informed decisions about when and how much to reorder, optimizing inventory levels and enhancing overall cost-effectiveness.
The Dropshipping Method
Dropshipping is an inventory management technique where retailers do not physically stock the products they sell. Instead, when a customer places an order, the retailer purchases the product in question from a third-party supplier. Then the third-party supplier ships it directly to the customer. This approach eliminates the need for holding inventory, reducing upfront costs and storage expenses. Dropshipping offers businesses greater flexibility and scalability. In this way, businesses can offer a wide range of products without the burden of maintaining a warehouse. However, it also comes with potential challenges, such as relying on supplier availability and potentially lower profit margins due to higher product costs.
Know About Inventory Management Solutions
Inventory management systems are crucial tools for businesses to track and control their inventory efficiently. Manual systems involve traditional, hands-on methods where inventory is recorded and monitored using pen and paper or spreadsheets. While cost-effective, manual systems are prone to human errors and are time-consuming. On the other hand, automated systems utilize software and technology to manage inventory data, streamlining processes and reducing errors.
Automated systems can automatically update stock levels, generate reorder alerts, and offer real-time insights for better decision-making. Cloud-based inventory management systems take automation a step further by storing data on remote servers accessible through the Internet. These systems offer real-time collaboration, scalability, and easy integration with other business tools. Moreover, they provide secure data storage and backups, reducing the risk of data loss.
Challenges of Inventory Management
To truly know about inventory management is to understand it comes with its fair share of challenges for businesses. Overstocking can tie up valuable capital and storage space. This leads to increased carrying costs and potential obsolescence. Of course, you can always count on long-term storage, but be careful how you store the items. Conversely, stockouts can result in lost sales, dissatisfied customers, and harm to the brand’s reputation.
Accurate forecasting is essential but can be difficult, as demand fluctuations, seasonality, and market trends make it challenging to predict inventory needs precisely. Additionally, inventory shrinkage, caused by theft, errors, or damage, can lead to unaccounted losses and reduced profitability.
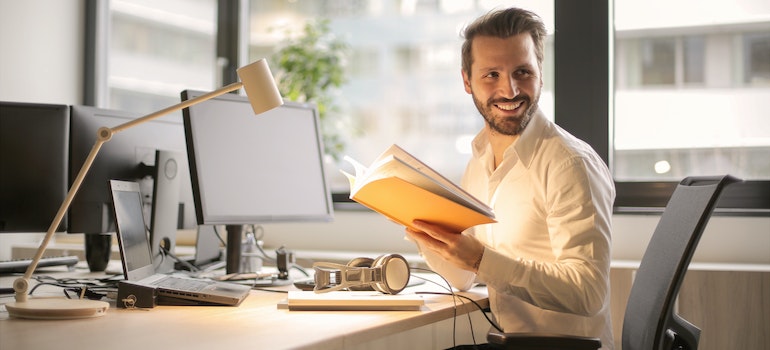
To overcome these challenges, businesses need to implement effective inventory control measures, adopt reliable forecasting methods, regularly assess inventory levels, and consider using advanced technologies and inventory control systems to optimize their inventory operations.
Incorporating the Best Practices
Incorporating best practices in stock management is essential for businesses to ensure operational efficiency and cost-effectiveness. Regular audits of inventory levels help identify discrepancies, prevent stockouts, and reduce the risk of inventory shrinkage. Effective supplier relationship management ensures timely deliveries, favorable terms, and competitive pricing, fostering a reliable supply chain. Embracing technology and automation streamlines inventory processes, enabling real-time tracking, demand forecasting, and automated reorder triggers.
Utilizing goods management software provides businesses with accurate insights and analytics, aiding in data-driven decision-making. Leveraging barcoding and RFID technology enhances inventory accuracy and expedites tracking. If using storage, consider safety measures when choosing a facility. By implementing these best practices, businesses can optimize their inventory control, minimize carrying costs, improve order fulfillment, and ultimately enhance customer satisfaction and profitability.
Inventory Management – A Crucial Aspect of Successful Businesses
Effectively controlling and optimizing inventory levels can lead to reduced costs, streamlined operations, and improved customer satisfaction. By implementing various asset management techniques, businesses can strike the right balance between supply and demand. Overall, adopting best practices in asset management empowers businesses to stay competitive, respond to market changes swiftly, and achieve sustainable growth in today’s dynamic business landscape. Since you are now familiar with everything you should know about inventory management, do not be afraid to use that knowledge.